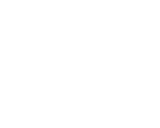
EAF OPTIMIZATION
FIELD SERVICES PRODUCTS
AMI technical experts are available on a contract basis
at your location or with remote monitoring.
We have the largest technical team in the world that is exclusively dedicated to EAF optimization. We believe that the best available technology must be offered with the highest level of service in order to achieve the full potential of your furnace operation. AMI has developed a presence with offices around the world, having guaranteed available contact with an engineering team based in different countries, providing immediate technical support for emergencies in every time zone.
TECH SUPPORT
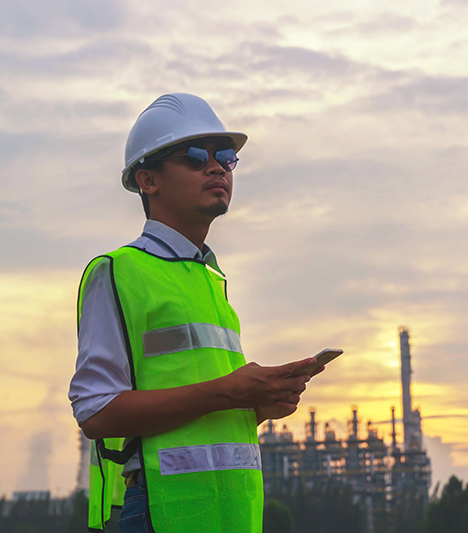
AMI technical advice and counsel applicable to the PLC, HMI equipment, training, system and process analysis and diagnostics, highly specialized background and experience in furnace optimization and operation.
FIELD ENGINEER
This service is defined as technical advice and counsel from field personnel based on good engineering, manufacturing, installation and operation practices as applicable to the PLC and HMI equipment. To the extent specified during performance of work, such services may also include analysis, adjustment, programming and other similar services.
REGULATION SPECIALIST
This service includes the technical assistance of personnel nor normally classified as field personnel for solving problems that require a highly specialized regulation background and experience including training, application design, power profile design, practices implementation, system and process analysis and diagnostics as required to complement the work scope.
EAF PROCESS SPECIALIST
This service includes the technical assistance of personnel not normally classified as field personnel for solving problems that require a highly specialized background and experience in furnace pptimization and pperation, including advanced control techniques training, application design, artificial intelligence, systems and process analysis and diagnostics as required to fulfill process operation benefits.
OPTIMIZATION AS A SERVICE (OPTaaS™)
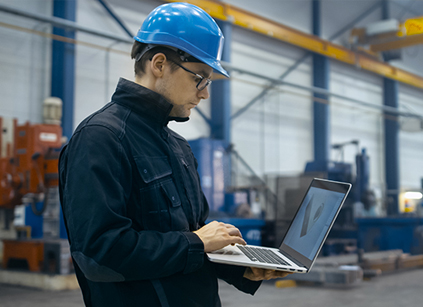
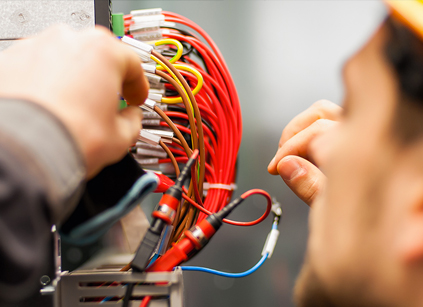
Our experience is that EAF Optimization should be understood as a service, and not as a product. In order to maintain and sustain the EAF performance improvements, AMI offers the EAF OPTaaS™ service to work closely with the customer on an on-going basis not only to maintain, but to improve the operating performance in time.
There are many variables in the EAF operation and in the process itself that need to be taken into consideration in the optimization task, for example:
Additionally, the objective of the client in the optimization task must be defined, whether the furnace should run on higher productivity, or better efficiency, to decrease operation cost. But mainly, we understand that these priorities change over time. When our specialists understand these conditions, they can set the rules for the EAF to run efficiently. Many experiences in optimization fail because the system deteriorates over time as the operational conditions change.
Our EAF OPTaaS™ is a comprehensive service package including the following components:
REMOTE MONITORING SERVICE
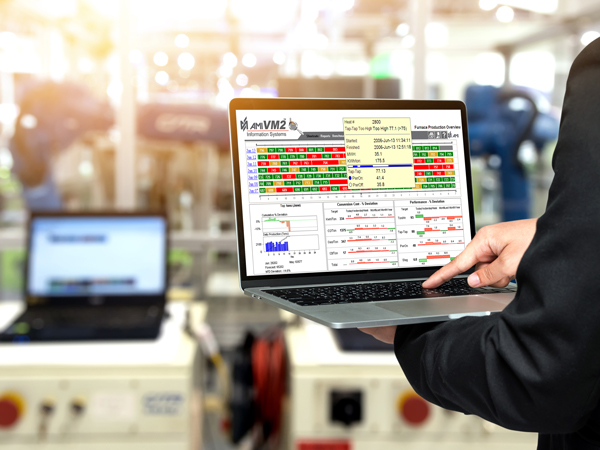
The Virtual MeltShop 2.0 (VM2 EAF) Remote Monitoring system is an AMI service that allows internet access of your EAF operational data. The available information can be accessed via internet using a standard web browser or a mobile device and can be organized into a number of standard and customized reports. Every installation of the DigitARC™ PX3 / SmartARC™ includes a VM2 Service trial free of charge for one year.
The system, already installed in several plants around the world, also gives full access to the AMI’s experts team and their valuable expertise to help you to monitor your operation and identify possible issues. All our observations are shared with you so that preventive actions can be taken anytime.
TRANSFORMER CARE SERVICES
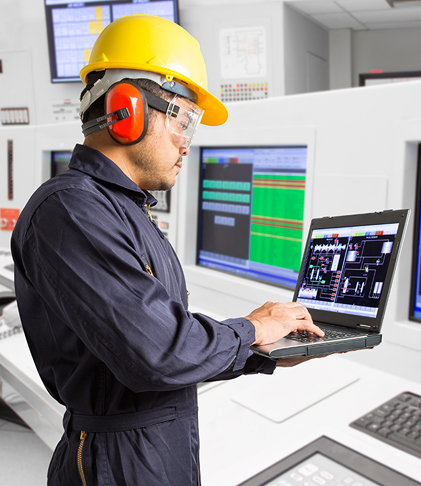
STUDIES:
Expert engineers develop Power Studies with the purpose of achieving Transformer Safety through several analyses. This way, our customers will obtain Arc Stability, and as a result, improve their EAF’s functionality. Transformer Care Power Studies identifies EAF Operation optimization opportunities with the High Impedance Concept.
SERVICES
Likewise, AMI offers Transformer Care Power Services. AMI engineers are constantly collaborating with our customers to keep their Transformers in good shape.